Achieving High-Quality Stainless Steel Pipe Welds
Stainless steel’s corrosion resistance, strength, and aesthetic appeal make it a popular material across industries. However, welding stainless steel pipe brings unique challenges compared to carbon steel. Stainless alloys are less forgiving, and flawed welds can undermine the material’s desirable properties.
Using proper techniques and an experienced welder is key to achieving strong. What goes into a high-quality weld? What pitfalls should be avoided? Below we’ll explore the key considerations for this success.
Choosing the Right Stainless Alloy
With many stainless steel grades available, it’s important to select one suitable for your application and the intended welding method:
-Austenitic Grades – Types 304, 304L, 316L are the most common. They offer good corrosion resistance and weldability. High heat input can diminish corrosion resistance.
-Ferritic Grades – Types 430 and 409 have good ductility but are more difficult to weld and more prone to cracking. Preheating is often required.
-Martensitic Grades – Type 410 offers very high strength but also low weldability and ductility. It requires highly controlled heat input to avoid cracking.
-Duplex Grades – Duplex stainless with a ferritic-austenitic microstructure has excellent strength while maintaining weldability. Common for high-pressure oil, gas, and chemical piping.
-Precipitation-Hardened Grades – These specialty alloys obtain very high strength through heat treatment after welding. Their superb strength comes at the cost of poor weldability.
Using the Right Filler Material
Choosing a compatible filler rod, wire, or electrode is also critical for quality welds:
-Match filler to pipe alloy – Use 308L rod for 304L pipe, or 316L rod for 316L pipe. Mismatched alloys risk reduced corrosion protection.
-Consider overalloying – Using a filler with more nickel than the base pipe improves weld penetration and guards against chromium depletion from oxidation.
-Watch ferrite content – Balance austenite and ferrite phases based on alloy grades to prevent cracking. Duplex stainless filler balances the two.
-Use matching coating – Flux-coated stick electrodes must pair with alloy grade to provide proper shielding and deposit chemistry.
Controlling Heat Input
Too much heat input during welding can negatively impact stainless steel’s properties:
-Prevent overheating – Excessive heat leads to chromium carbide precipitation, reducing corrosion protection. It also promotes grain growth, embrittlement, and distortion.
-Use lower amperage – Reduce current levels to the minimum needed for penetration. High heat input comes from using too much current.
-Limit interpass temperature – Allow the joint to cool between weld passes. A maximum interpass temperature of 350°F is recommended.
-Use pulsed MIG – Pulsing the arc in MIG welding concentrates heat input. This results in better control compared to traditional CV MIG.
Preventing Porosity
Trapped gases in the solidifying weld create pores and cracks detrimental to quality:
-Remove contaminants – Any grease, oil, paint or dirt on joint surfaces traps gases and must be thoroughly removed first.
-Use gas shielding – Shield the weld pool from oxygen exposure using argon or other inert gas to prevent oxidation porosity.
-Avoid turbulence – Excessive arc length variation stirs the weld pool and leads to gas entrapment. Maintain steady travel speed.
-Check grounding – Inadequate electrical contacts or workpiece grounding also introduce arc irregularities. Securely ground parts near welds.
Minimizing Corrosion Risks
To retain stainless steel’s corrosion resistance, care must be taken:
-Prevent carbon pickup – Carbon from coatings or the atmosphere creates carbides reducing chrome availability for corrosion protection. Use clean material and low-carbon fillers.
-Use back purge gas – Shield the pipe’s inner weld seam from oxidation using argon back purging. This prevents corrosion on the pipe’s interior surface.
-Remove heat tint – The thin discolored layer from welding heat lowers corrosion resistance. Removing it via pickling or mechanical grinding restores the original surface.
-Clean between passes – Wire brushing or other cleaning between passes prevents accumulated debris from contaminating the next weld layer.
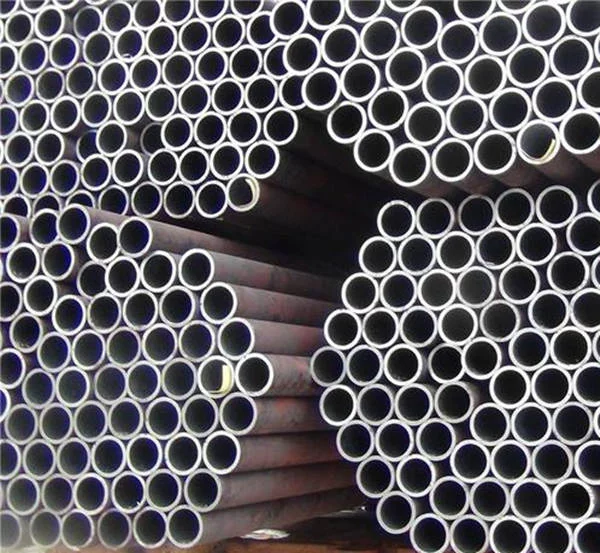
Avoiding Other Defects
Proper welding technique also avoids flaws like:
-Lack of fusion – Incomplete blending between weld and base metal, often from low heat input. Causes joint weakness.
-Incomplete penetration – Full penetration of weld into the joint edges is critical for complete bonding. Lack of penetration creates leak risks.
-Undercut – Melting of the base metal surface decreases thickness. It concentrates stresses and provides crevice corrosion sites.
-Distortion – Unbalanced heating and cooling causes weld joint movement. Fixtures may be needed to minimize distortion of thin-walled stainless pipe.
By understanding the unique needs of stainless alloys during welding, fabricators can achieve the high-quality, long-lasting welded joints required in critical applications. Proper welds maintain corrosion resistance and prevent leaks over the full service lifetime.